2018 hat Audio Service die Produktion von Im-Ohr-Hörsystemen von Deutschland nach Polen verlagert, seit 2021 auch die Produktion der Atelier-IdOs: Im European Manufacturing Center (EMC) in Poznań kann dank optimierter Prozesse eine größere Auftragslage bewältigt werden. Allerdings berichteten Hörakustiker bald schon von Auswirkungen auf die bislang gewohnte Qualität. Heute, so versichert Michael Weitkamp, gibt es dazu jedoch keinen Grund mehr. Der Leiter des technischen Kundenservices bei Audio Service erklärt, wie die IdO-Fertigung abläuft – und wie Qualität und Kundenzufriedenheit sichergestellt werden.
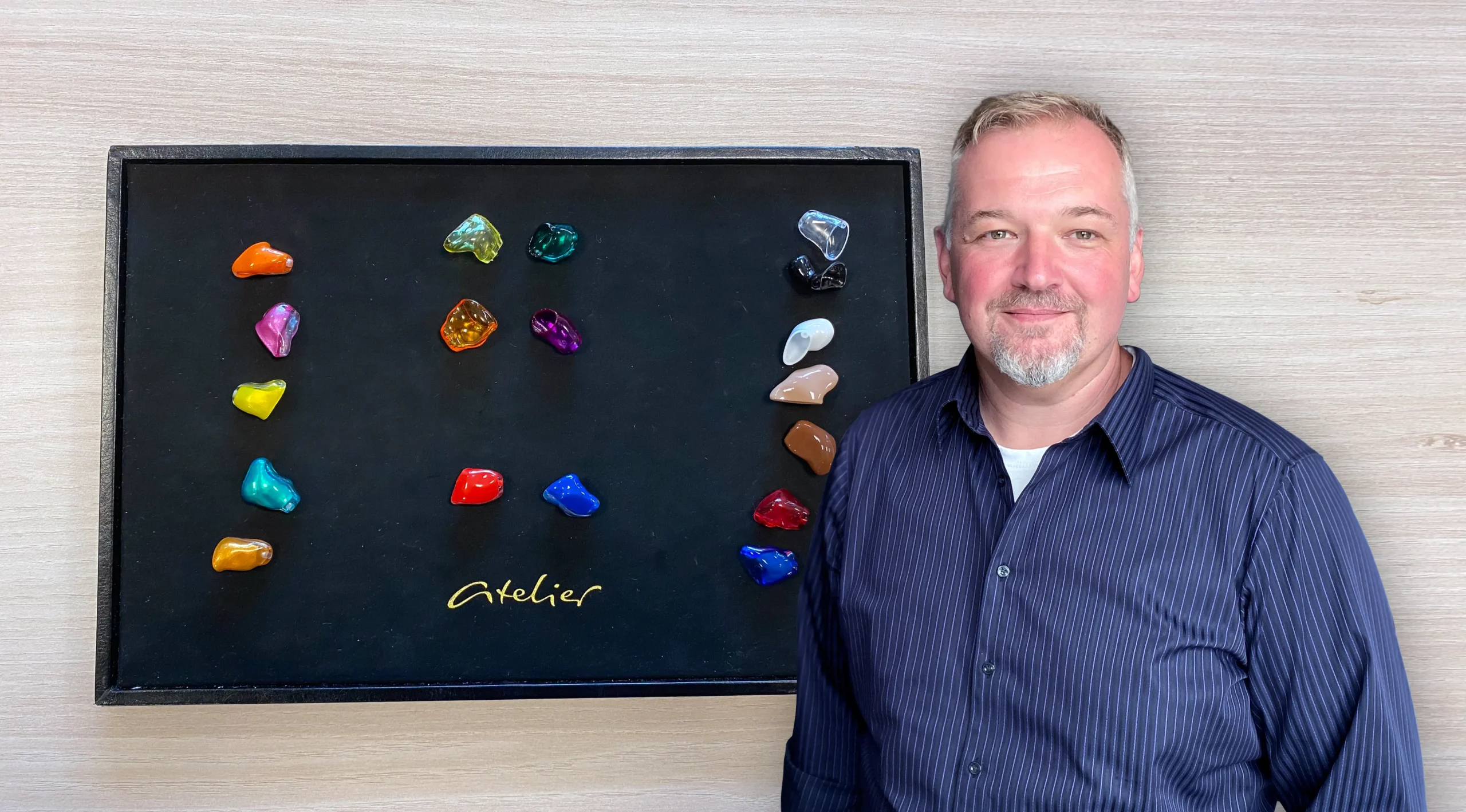
Michael Weitkamp ist Leiter des technischen Kundenservices bei Audio Service. Und er gibt den Akustikern recht – zumindest teilweise: „Es ist nicht alles rund gelaufen.“ Man habe sich erst einmal an die Arbeitsweise in Poznań gewöhnen müssen. „Früher hatte man alles in seinen Händen. Da konnte man vieles individuell lösen. In Poznań ist jedoch alles sehr prozessorientiert – diese Prozesse muss man erst einmal verstehen und sich an sie halten, nur dann ist nachvollziehbar, wo es klemmt. Heute haben wir das im Griff“.
Schritt für Schritt: Der Weg zum Audio Service-IdO
Die Entscheidungsgewalt liegt nach wie vor bei Weitkamps Team in Löhne. „Das gilt für alle IdOs, nicht nur für Atelier“, betont er. Zwar schickt der Hörakustiker den physischen Abdruck über Krefeld nach Poznań, allerdings wird er dort lediglich eingescannt und zur Plausibilitätsprüfung nach Löhne geschickt. Digitale Scans schicken Hörakustiker direkt zum deutschen Standort.
Erst nach der Bearbeitung und gegebenenfalls Klärung durch das Team in Löhne beginnen die Mitarbeiter des EMCs mit dem Modelling der regulären IdOs mit festem Tech Level. Die Atelier-Modelle bleiben in Deutschland. „Hier sind drei Mitarbeiter beschäftigt, die sich um das Modelling der Atelier-Geräte kümmern. Das ermöglicht zum Beispiel die direkte Klärung von Rückfragen: Während des Modellings kann man dann mit dem Akustiker telefonieren und Änderungen live vornehmen“, sagt Weitkamp.
Eigene Fertigungsstraße für Atelier-Hörsysteme
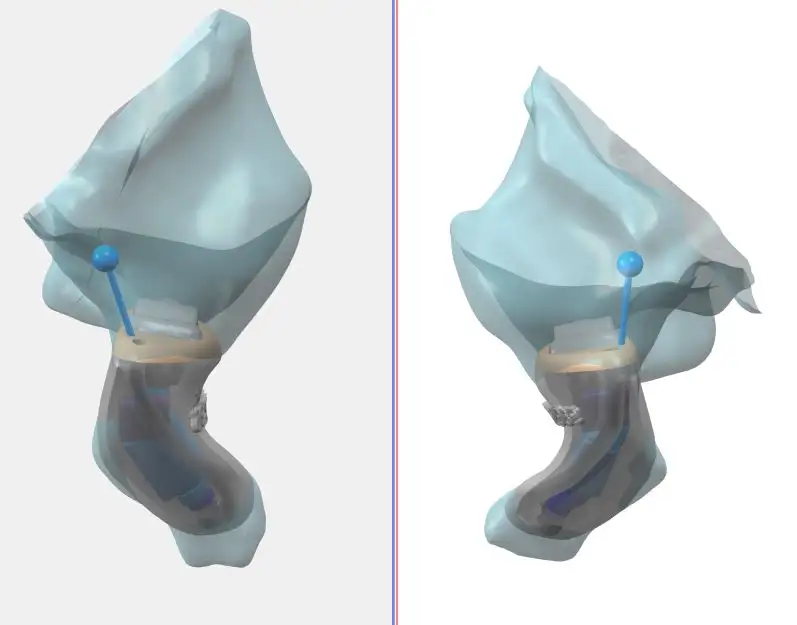
„Sobald das Modelling der Atelier-Modelle abgeschlossen wurde, erhält der Hörakustiker eine Mail mit einem Screenshot des modellierten Auftrags und kann dann zur Not nochmal einhaken. Möchte er detailliertere Infos, weil er beispielsweise noch etwas mit dem Endkunden besprechen möchte, kann er uns das vorher mitteilen. Dann wird der Auftrag nach dem Modelling geparkt, es werden Screenshots mit mehreren Ansichten versendet und das Modell geht erst nach der Freigabe des Akustikers zur Fertigung ins EMC“, erklärt Michael Weitkamp.
In Poznań angekommen, geht es mit der Schalenfertigung weiter. Den Atelier-Modellen steht dafür eine eigene Fertigungsstraße zu: „Dort werden ausschließlich Atelier-IdOs bearbeitet. Die Mitarbeiter haben hier außerdem 30 Prozent mehr Zeit für jedes einzelne Hörsystem.“
5 Tage von Auftragseingang bis zum Versand
Apropos Zeit: Vom Eingang des Abdrucks bis zum Versand in Poznań vergehen etwa 5 Tage – je nach Auftragslage auch mal zwei mehr oder weniger. „Alle Aufträge, die bis 15:00 Uhr eingehen, werden spätestens am Folgetag modelliert, ein Großteil noch am Eingangstag. Auf Wunsch realisieren wir auch Expresstermine“, sagt Weitkamp. Diese Zeitangabe gilt für alle IdO-Modelle: egal ob Atelier oder regulär.
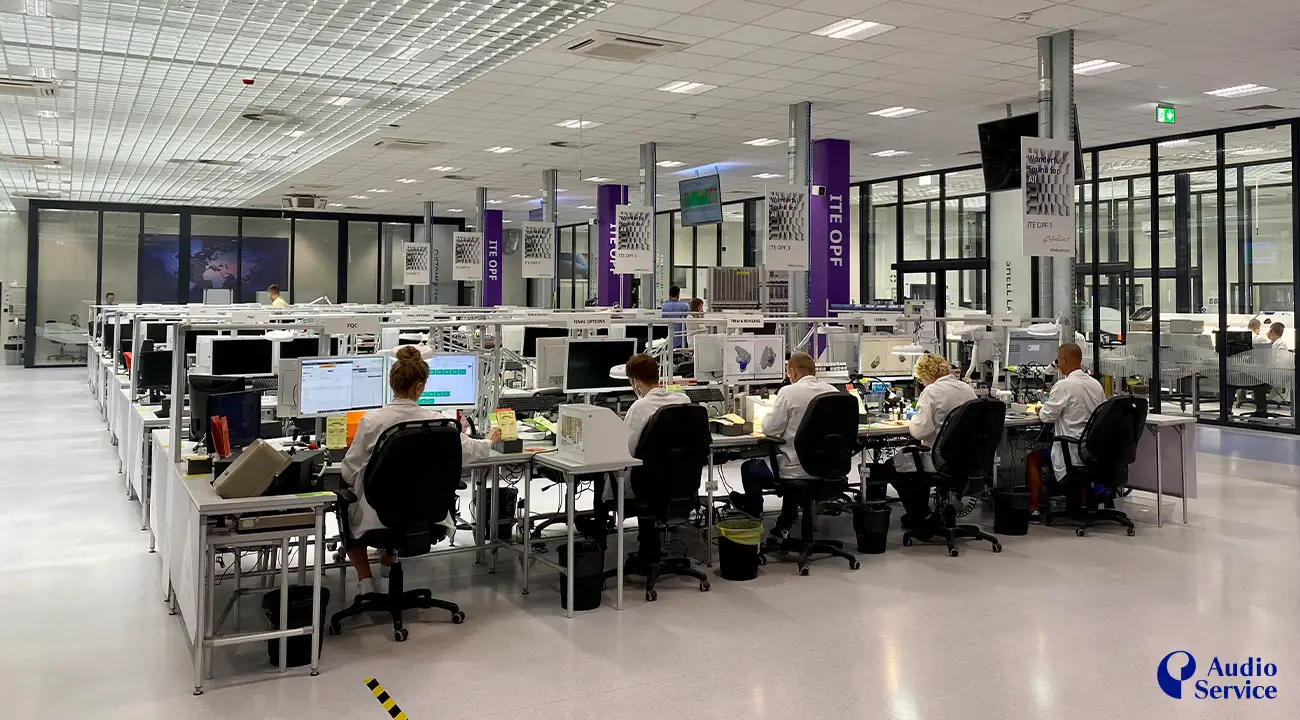
„Wir sind auf das Feedback der Akustiker angewiesen“
Dass Fehler passieren, komme leider immer wieder mal vor, sagt Michael Weitkamp. „Wichtig ist nur, dass Hörakustiker auf uns zukommen, wenn Unmut aufkommt. Man muss dann schauen, wo Fehler verursacht worden sind. In der Ersterfassung, der weiteren Auftragsbearbeitung, der Produktion, oder gibt es ein technisches Problem? Da sind wir auf das Feedback der Akustiker angewiesen.“
In Notfällen hat das Team in Löhne immer noch die Möglichkeit, Probleme abzuwickeln – zum Beispiel, wenn das Gerät kurz nach der Anpassung ausfällt, oder es wiederholt technische Probleme gibt. Der Akustiker sendet das defekte System nach Rücksprache direkt nach Löhne, wo dann sofort nach Eingang ein komplett neu gefertigtes Gerät mit gleicher Seriennummer in Arbeit gegeben wird. „Parallel dazu wird das kaputte Gerät an die Qualitätssicherung in Poznań geschickt. Dort kann es dann ohne Zeitdruck analysiert werden: Ist ein Bauteil defekt? Oder gab es einen Fehler beim Zusammenbau? Dann kann gezielt der jeweilige Mitarbeiter kontaktiert und nachgeschult werden.“ Jede Reklamation wird im System dokumentiert. Auf diese Weise können auch Trends erkannt werden, auf die man dann entsprechend reagiert.
Die beiden Standorte haben sich aufeinander eingestimmt. „Mittlerweile funktioniert es genauso gut wie früher“, sagt Michael Weitkamp. „Der einzige Unterschied: Wir haben das Gerät und den Papierauftrag nicht mehr physisch in der Hand, sondern virtuell.“ Jeder Prozess ist nur so gut, wie das Engagement all seiner Teilnehmer – vom Hörakustiker, über das Team in Löhne, bis zum EMC in Poznań. Greift alles ineinander, hält der Endkunde schlussendlich ein Hörsystem von der Qualität in der Hand, wie man sie seit jeher von Audio Service gewohnt ist.